Applications
Continents
Nations
Plants
Ceramic Fuse Production Line
Machine with 2 rotary index tables, for a total of 46 workstations.
- Production speed of 40 parts per minute
- Over 30 electric axes
- Six vision systems
- Over 1500 digital and analog I/O points
In addition to the complete management of the machine, we developed the system for production batch planning and reporting, product traceability, and a fully automated interface with the MES plant system.
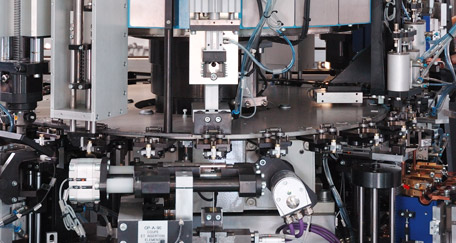
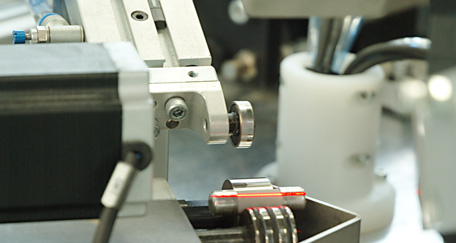
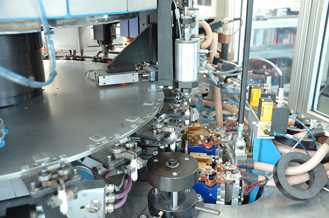
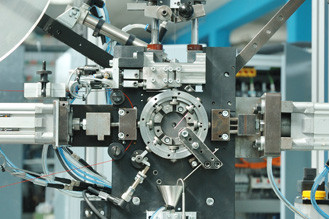
Control Machine for Spray Pump Pins
In-line quality control machine
- High-definition vision system with pericentric optics
- Precision of 0.02 mm
- Cycle rate of 50 parts per minute
The use of advanced vision technologies has allowed us to optimally control the quality of the part. The pericentric optics used narrowed the field of view to just 5 mm per side; this made it possible to measure the ovalization of the part with an accuracy of 0.04 mm. Other traditional control stations were able to ensure quality control of all the technological aspects of a very small yet crucial part for the final product’s performance.
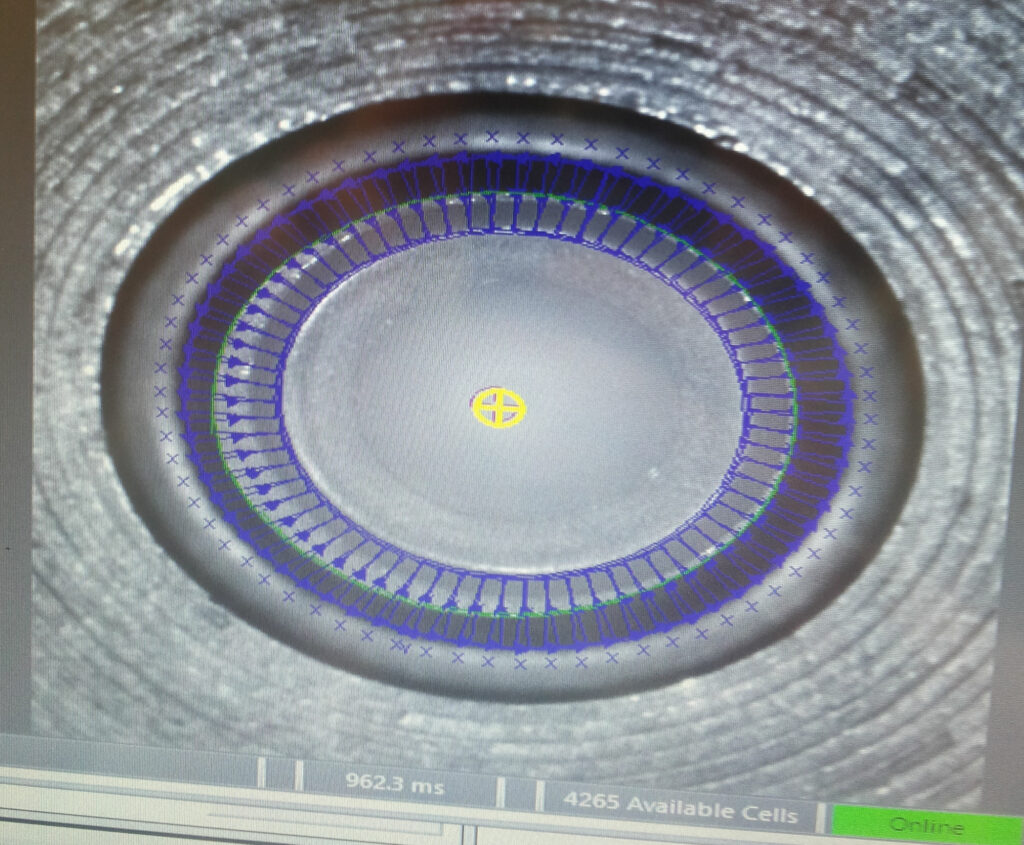
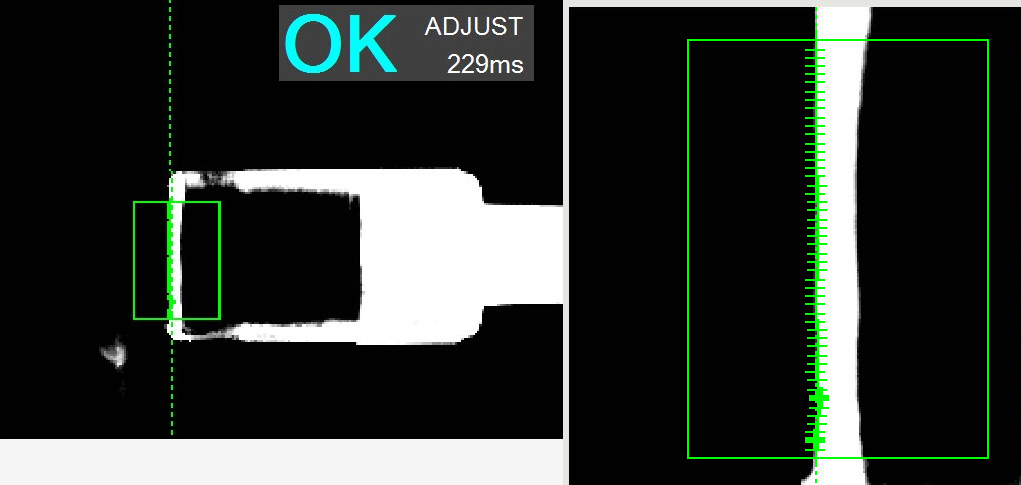
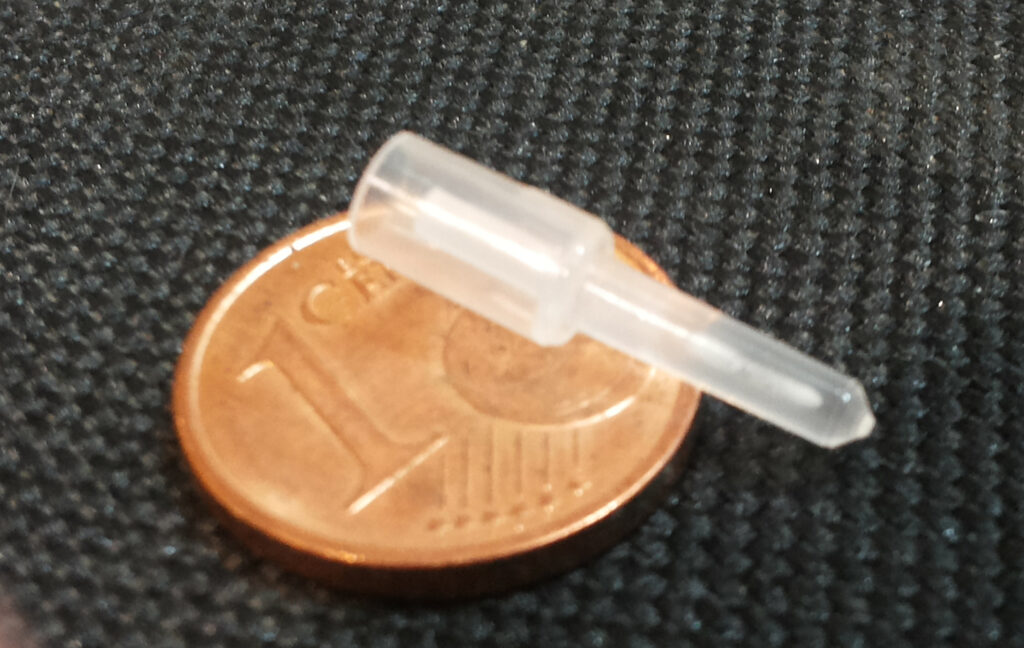
Control System for Drywall Panel Profiling
Dimensional control of the panel in the production line
- Product speed under the control station: 90 m/min
- Data sampling rate: 10,000 samples per second
- Ability to determine the thickness of the panel at every millimeter of the inspected area
- Control of edge profiles and their thinning
The instrument has replaced a destructive sample control, which was carried out on average once or twice an hour. This has allowed for an increase in product quality by enabling timely corrective actions before process deviations occur
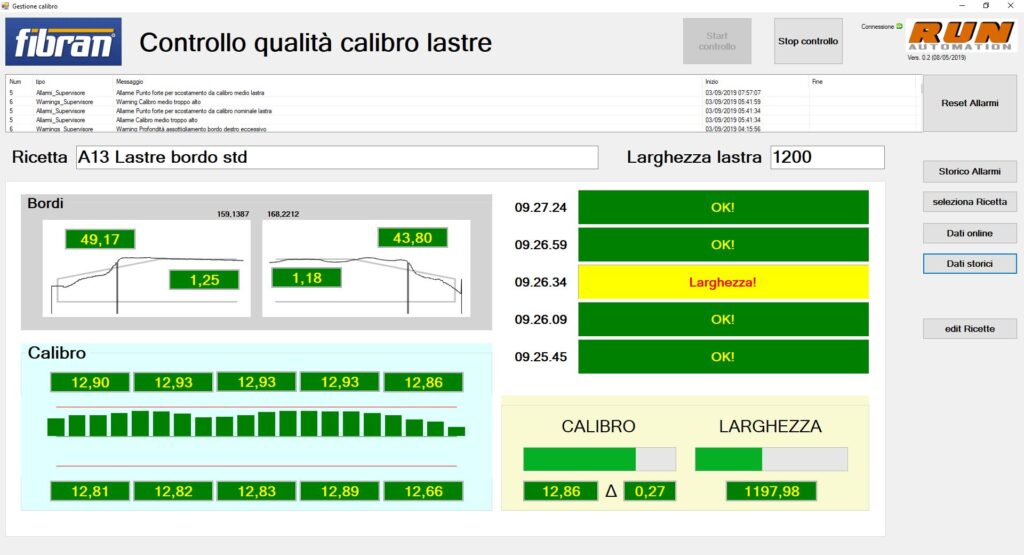
Complete Revamping of the Drywall Production Line
Complete design of the electrical system, fully replaced
- Complete development of the operational software for the plant
- Development of new human-machine interfaces
- Implementation of a complete supervision system
The complete overhaul of the electrical project, the full replacement of the automation panels and the electrical system, and the integration of new-generation continuous dosing systems have transformed a dilapidated plant into one with more than doubled production capacity, achieving efficiency of over 90%.
All the work was carried out step by step, and the plant was never inactive for more than three consecutive days, thereby ensuring constant production and planning for a sustainable investment.
Self-propelled Rock Salt Extraction Machine
Revamping of a Voest-Alpine milling machine used in mining for the extraction of rock salt for food use. The machine is particularly sensitive in its hydraulic precision movements and is subjected to significant stresses in a very harsh environment. It is equipped for remote control from the ground and for real-time production data collection.
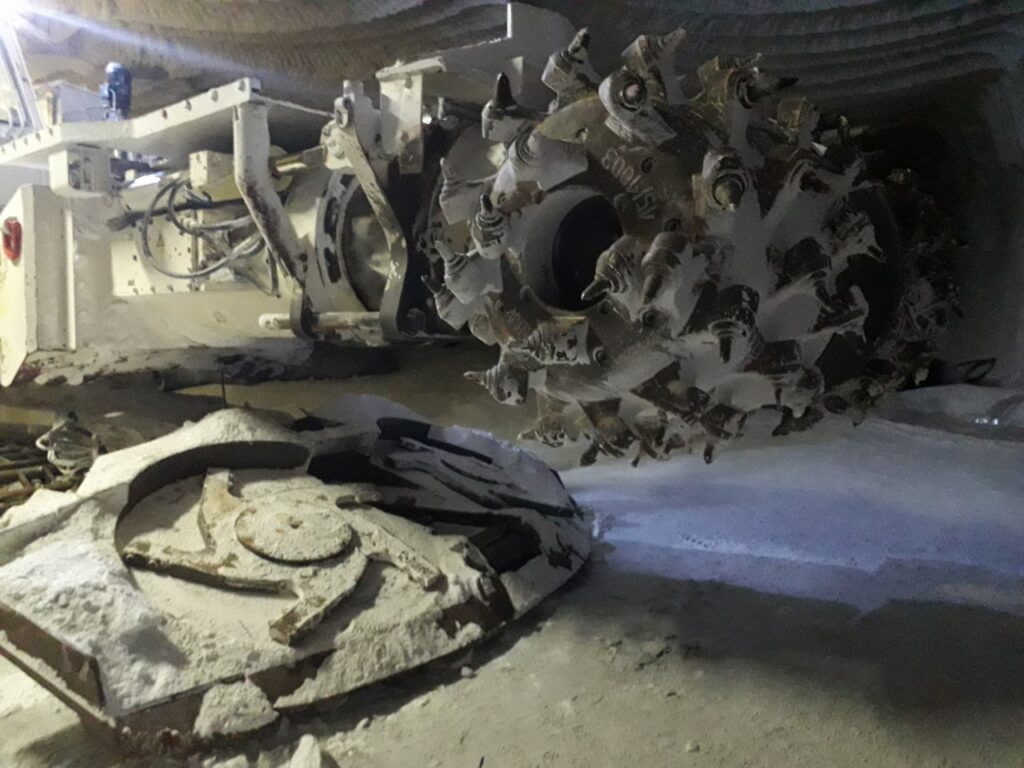
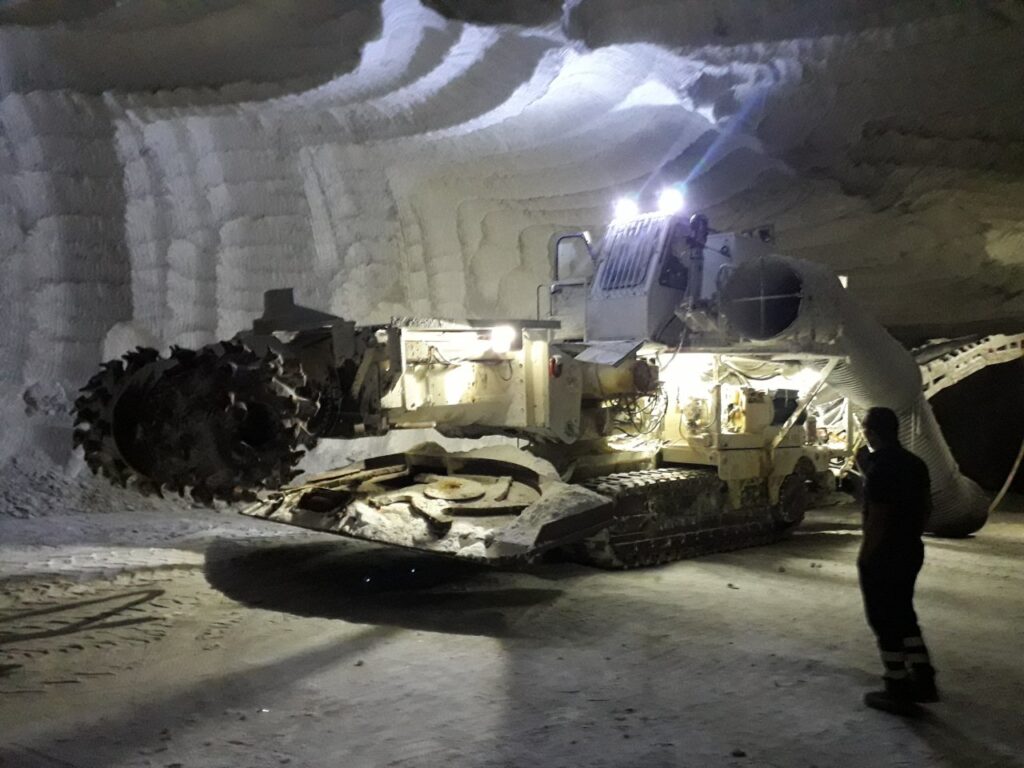
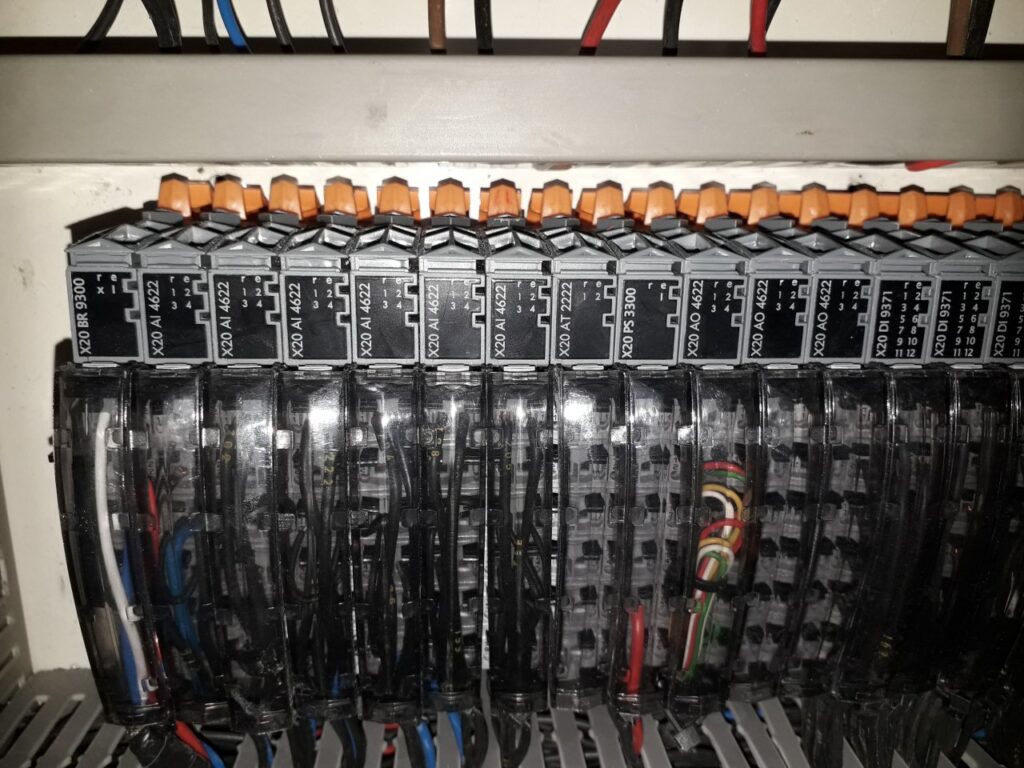